Day 1: Tuesday, May 20
Module 1: Pellet Preparation & Conditioning
8:30 am – 9:00 am
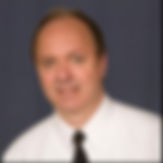
Precision and Repeatability in Dosing Additives, Specifically Color
Speaker: Alan Landers, Product Manager | Conair
Precision and repeatability in additives, specifically color – when it comes to extrusion of film, sheet, and fiber. This session will talk about the necessity of trending, tracking, and tracing additive usage, to verify the perfect repeatability in demanding film, sheet, and fiber extrusion processes. Not only can the proper equipment produce perfect color match shift after shift, but it can result in ROI in weeks, not years.
9:00 am – 9:30 am
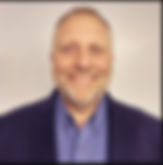
Energy Efficiency Considerations for Extrusion
Speaker: Joe Dziedzic, Sr. Product Manager | ACS Group
The presentation will discuss some simple and cost-effective changes to the Extrusion process that can reduce overall operating costs, improve plant safety and improve the overall bottom line and profitability.
Module 2: Melt Preperation & Delivery
9:30 am – 10:00 am
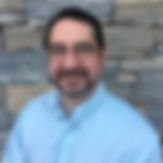
Solids Conveying: The Differences in Smooth Bore vs. Shallow Grooves vs Full Grooves
Speaker: Kevin Slusarz, Dir. of Process Technology | US Extruders
The pros and cons of each type of feeding section (smooth bore barrels, barrels with shallow grooves, and barrels that are fully grooved) will be addressed in this presentation.
10:00 am – 10:30 am

The Role of Melt Temperature, Melt Pressure, and Mixing in Extrusion
Speaker: Chris Rauwendaal, President | Rauwendaal Extrusion Engineering
This presentation will be an overview of the role of melt temperature, melt pressure, and mixing in the extrusion process and the interdependency of these parameters. Factors that affect melt temperatures will be analyzed as well as the prediction of melt temperatures. We will discuss why pressure measurement is important and what factors determine melt pressure. We will elaborate the basic mixing principles and why mixing is critical in the extrusion process. Finally, we will discuss how to achieve efficient distributive and dispersive mixing.
Break
11:00 am – 11:30 am

Ultra-Fine Mixing and Its Results
Speaker: Keith Luker, President | Randcastle Extrusion Systems, Inc.
A new screw design avoids the primary cause of surging using a series of mixers; each mixer dampens the volumetric input variation yielding very fine pressure control.
11:30 am - 12:00 pm

Practical Screw and Barrel Design for Venting in a Twin-Screw Extruder
Speaker: Kenneth Russell, Sr. Principle Engineer |SACO AEI Polymers
Venting is necessary in some compounding and most reactive extrusion operations to remove reaction by-products and unconverted reactants. Often venting is necessary to ensure that the density of the extrudate is within the required limits. However, operational problems can arise at the extruder vent. Issues such as vent flow, condensate carry over, and plugging can cause process upsets and create quality and safety issues. Many of these issues can be mitigated with the design of the screw configuration in the vented region.
Lunch
1:00 pm – 1:30 pm

Reactive Extrusion: An Overview
Speaker: Carlos Escobar, Research Scientist | Dow
The objective of this presentation is to provide an overview and best practices of how to use Reactive Extrusion to produce polyolefins with reactive functionality.
1:30 pm - 2:00 pm

Managing Melt Pressure & Temperature in a Twin-Screw Extruder
Speaker: Brian Haight, Technology Manager, Leistritz Extrusion
Polymers are typically melted to facilitate processing goals, such as mixing, devolatilization and pumping. During these processes, some polymers and additives will degrade when exposed to elevated temperatures. Managing both pressure and time at temperature exposure becomes important to help mitigate this issue. Various techniques to successfully process thermally sensitive materials via twin screw extrusion with supporting test results, will be presented to help gain insight how to process these formulations.
2:00 pm - 2:30 pm

Mixing in Single-Screw Extruders
Speaker: Tim Womer, President | TWWomer & Associates, LLC
Mixing with single screws is a very critical part of a good screw design. Understanding the type of mixer needed for the resin being processed is most important. Should a distributive or dispersive mixer be used or should both types be used? All single screws should have a mixer, even if natural or pre-color resin is being processed. These topics will be discussed during this presentation.
2:30 pm - 3:00 pm
Optimizing Downstream Filtration and Pumping
This presentation will delve into various options in filtration/screen changer, and melt/gear pump technology to optimize melt quality feeding the die.
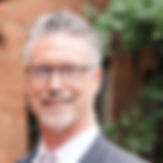
Speaker: Dana Darley, President | Dana Darley Extrusion Solutions, Inc.
Break
Module 3: Instrumentation
3:30 pm - 4:00 pm

Guide to Drive and Control Upgrades for Extruders
Speaker: Scott Barlow, Founder | Integrated Control Technologies
Integrated Control Technologies has developed "A Guide to Upgrading Extruders for Everyone" in order to assist plastic manufacturers in creating a plan for how to have a successful extruder upgrade. Whether your role is coporate engineer, plant manager, plant engineer or plant maintenance, we believe that you will find the infromation useful. This presentation will take you through those important steps of this process.
4:00 pm - 4:30 pm

Preparing Extrusion Data for AI
Speaker: Peter Brand, COO & Co-Founder | Oden Technologies
Many manufacturers are looking to invest in AI to improve production. However, unlike other industries that can pull from traditional databases to use in AI models, manufacturers have extremely specialized needs when it comes to packaging their data for effective use in AI.
4:30 pm - 5:00 pm

AC Drive (VFD) Technology Trend in Extruder Market
Speaker: Sean Kim, Dir. OEM Sales General Machinery & Extruder
US Motion Business ABB
This presentation will explore the latest technology advancement in AC Drive (VFD) technology, particularly focusing on industrial automation applications. Highlighting some advance features like seamless integration of industrial communications, safety options, and harmonic mitigation. Overviewing some of VFD advancement for future smart manufacturing consideration.
6:00 pm - 8:00 pm

Extrusion Conference Opening Reception at the Sam Adams Boston Taproom!
Cheers! All registered attendees are invited to join us after a day of sessions for happy hour, food and fun!
Day 2: Wednesday, May 21
Module 4: Die Design Fundamentals
8:00 am – 8:30 am

Blown Film Die Design Principles Every Processor Should Know
Speaker: Karen Xiao, VP of Technology | Macro Engineering & Technology, Inc.
This presentation will give a general overview of blown film die design principles, introduce the types of blown film dies in the industry and the factors that are important in evaluating the performance of blown film extrusion systems that every processor should know.
8:30 am – 9:00 am

Profile Die Design Principles
Speaker: Randy Brown, Independent Consultant | IPlasticPI
- Rheology – Top Consideration when designing profile extrusion dies
- Design methodology to achieve a good part
- Cooling is critical to achieving a good part
- Tuning in a Profile Die
9:00 am – 9:30 am

Tubing Die Design Principles Every Processor Should Know
Speaker: John Perdikoulias, Vice President |Compuplast
There are some basic flow and process characteristics that need to be considered when design a tubing die and process. The design process begins with the required product dimensions (O.D. and Wall thickness). Once this is specified, the output or line speed will be determined by the extruder and cooling capacity. At this point, we should verify that the extruder can produce a good quality melt for the available cooling rate. Once we have determined the output rate and melt temperature, then we can begin the process of optimizing the die and flow channels after the extruder. This presentation will show this engineering process using 3 different types of tubing dies and explain the design criteria that need to be maintained to ensure product quality, maximize production and minimize down time for cleaning.
9:30 am – 10:00 am
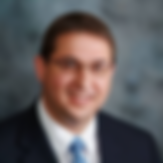
Flat Die Design Principles and Enhancements
Speaker: Sam Iuliano, Chief Technologist | Nordson Dies Industries, LLC
Presentation topics: how flat dies work, basic construction, flow distribution manifolds, slot gap and width adjustments, basic and enhanced distribution tuning adjustments
Break
Module 5: Processing Challenges in a Sustainable World
10:30 am – 11:00 am

Bioplastics Processes: Mixing and Devolatilization via Twin-Screw Extrusion
Speaker: Charlie Martin, President/GM | Leistritz Extrusion
Presentation Key Topics:
-
How to mix heat and shear materials without degradation in a twin screw extruder
-
Tips and theories for effective devolatilization
-
How to stage unit operations along the length of the twin screw extruder process section
-
Upstream and downstream options and configurations
11:00 am - 11:30 am
Overcoming Sheet Extrusion Challenges Associated with Biopolymers and PCR Resins
Speaker: Tom Limbrunner, VP - Applications & Technology | PTi
To meet sustainability goals, processors must first understand the challenges associated with biopolymers and PCR. This presentation demonstrates how high vacuum twin-screw multi-resin extrusion technology best supports the processing of hygroscopic materials, such as PET/PLA and PCR (especially those laminated with Polyolefin, PET, PETG, etc.).
11:30 am - 12:00 pm

Closed-Loop In-line Color Correction Automation When Extruding PCR & PIR
Speaker: Douglas Brownfield, Commercial Dir. of CISystems | Ampacet Corp
New automation that allows PCR compounders and extrusion companies running high rates of PCR or PIR that takes the line operator out of color QC and no longer responsibile for maintaining color standards during production. New Ai color correction software and hardware that measures color in-line and corrects color in-line with individual mono pigments in real-time.
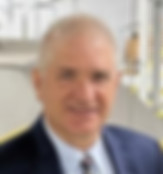
Lunch
1:00 pm - 1:30 pm
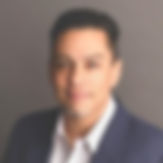
Enhancing Efficiency in Extrusion: Advanced Purging Techniques for Sustainable Operations
Speaker: Lenny Gutierrez, Technical Sales Rep |Asaclean-Asahi Kasei Plastics NA
This session explores advanced purging techniques to tackle common extrusion challenges like contamination, material buildup, and extended changeover times. Learn how optimized purging practices can enhance efficiency, reduce waste, and contribute to more sustainable operations.
1:30 pm - 2:00 pm
Process Control in Foam Extrusion

Speaker: Dave Molloy, Dir. of Business Operations | PROMIX Solutions LLC
Accurate process control is necessary for the best foam quality, optionally fully or partly based on recycled materials. Any extruded foam product benefits from maximum homogenization of the melt, stable temperature conditions in the process and especially at the outlet at the die. This way continuously stable products are produced, and maximum material savings can be achieved at required performance. The presented paper presents a unique mixing cooler device featuring such process control.
Inline viscosity measurement additionally helps with the evaluation of the process, in terms of raw materials and product quality control, thereby preventing unnecessary scrap generation. Variations of process conditions are immediately displayed, e.g. via moisture content monitoring, temperature changes, filler dosing level, and reactive compounding conversion efficiency. The presented solution allows for the evaluation of all melt-based materials, ensuring full monitoring of the extruded product.
2:00 pm - 2:30 pm

One-Step Extrusion of PCR Resins title
Speaker: Monika Gneuss, Vice President | Gneuss
This presentation will cover a novel system for reprocessing of industrial and post-consumer waste from all kinds of polymers.
Break
Module 6: Trouble Shooting in Extrusion
3:00 pm - 3:30 pm

Expert Tips on How to Overcome Process Limitations in Your Compounding Line
Speaker: Cameron Kheradi, Dir. Process Technology | Coperion
This presentation will highlight common rate and quality limitations on twin screw compounding equipment, and provide insights on how to overcome them. We will follow the pellet through the individual unit operations from feed intake to pressurization and discharge.
3:30 pm - 4:00 pm

Flat Die Troubleshooting Tips
Speaker: Christine Ronaghan, Director Technology Group | Cloeren Inc
This presentation will cover a few specific case studies to guide processors in common troubleshooting efforts as they relate to flat die performance and optimization.
4:00 pm - 4:30 pm
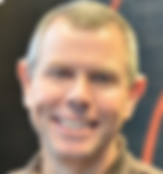
Solving Fluctuating Extruder Torque/Amps in a Co-Rotating Twin Screw Extruder
Speaker: Albert Bailey, Sales Engineer | ENTEK
This presentation will take a look at the reasons for entruder torque/amp fluctuations. As well the troubleshooting steps to combat these issues.
4:30 pm - 5:00 pm
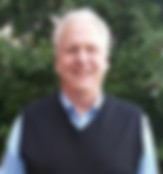
Identifying Wear Problems That Cause Downtime, Scrap and Lost Production
Speaker: Steve Jackson, Director of Sales | Extreme Coatings
This presentation will focus on adhesive wear, abrasive wear and corrosion, and will discuss how they manifest themselves.